Sumo bots
The driving idea behind the project was to create a system for children to be able to design and build their own robotic attachments in order to learn problem solving in the form of games and challenges. This would be targeted towards older (14-18+) teenagers as it would feature a guided design process of modelling, fabricating, and competing to test their designs.

I was in charge of designing parts for the robots, the parts were meant to have a modular system so kids can build different parts and experiment with them. The original plan is to make a few prototypes and eventually find a way to make these parts modular, but we ran out of time before being able to do so. So, while the parts were able to fit on the mbot2, we were unable to achieve the goal to make this modular, but since this is a demonstration, we decided that this is fine as a proof of concept.
The 3 parts designed were meant to represent 3 types of play style, one for defense attack and the last is for more skill expression.
​
​
​
​
A pincer-like design was made for skill expression as the parts have interconnected joints that allows the pincer to close when something hits the bumper and release when backing off. On the first iteration, we discovered some major flaws in the design as some pins were too fragile and the range of movement is too small, and the claw will not close when reversing. On the second iteration, most of these problems are fixed, but we still find flaws in the design as there was too much friction and the claws do not close evenly, but overall, this proof of concept is considered a success.
​
​
​
​
A ramp design was made for a defensive playstyle, this design does not have any moving parts except for the auxiliary wheels at the front. The first design worked, but we still thought that not having a part in between the ramp would cause weakness, so on the second iteration we added a part in between along with wheels to decrease friction to the ground. On a conceptual level, this design worked the best and was the only design able to flip over other mbots.
A crane like design was made for an aggressive play style, but we ran out of time and only one iteration was made and did not function as expected, the base can be used in many ways.



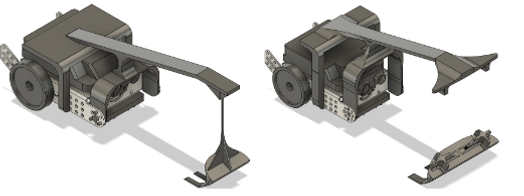
Design Process
Due to the nature of this assignment and having five group members to put this project together, our design process consisted of a lot of components being designed in parallel to each other. Although this was quite an efficient method, we had to be careful to consider other group members' work to ensure it would all work together seamlessly at the end.
The design was inspired by the HG 1/144 scale TR-6 woundwort plastic model kit from Bandai. The design has a semi modular system, there are parts with adapters which allows the integration of other model kits with 3mm holes. Along with TR-6’s slim design which allows a wide variety of parts placement, but the more parts added the more fragile the model kit becomes. Fragility does not matter much in model kits as the model acts as a decoration and is not meant to be played with like toys, taking this into account we want our parts to be more rigid and stable.
​


Manufacture and Construction
The manufacture and construction of this project required a series of 3D prints, support material removal, some laser cutting, cardboard/polystyrene cutting and way too much masking tape. The process is outlined below.
​
A considerable time was spent optimsing and restructuring the parts for 3D printing in order to make them small enough, strong enough, easy post processing, and able to be assembled.
First iteration construction:
We found that the pins that fit on fine in fusion ended up being too large in reality and some need to be thicker to be more stable. And only 3 – 4 pins connected on each side is enough for stability. Also, the pincer needs to be larger to catch other mbots. The crane base needs to be taller as the mbot model in fusion is slightly shorter than in reality.
Second iteration construction:
The parts fit on great, the ramp may be slightly tight but will still fit without any issue while the pincer requires a small amount of glue to hold stable and the crane needs a lot more work. The 3D printing process has deformed parts of the ramp design, so to cover up rectangular pieces of black cardboard was cut up to cover the imperfection, while the cardboard did come off after 10 extensive battles, but the design still works as intended.